5 ∆® – Improvement of productivity and efficiency in production
The ‘5∆ Analysis and Optimisation of Work Processes’ method is one of the key techniques for ensuring continuous progress in a company.
Our project approach, the improvement and integration of innovative activities, the establishment of methods to measure and monitor progress, as well as the setting up of a system for recognising value-added work, result in efficiency improvement in production and logistics.
The method is used in conjunction with the introduction of ‘LEAN MANUFACTURING’ and ‘WORLD CLASS MANUFACTURING’ concepts.
‘5∆’ method combines in a coherent manner different methodologies, both our own as well as others already known:
- 5 S
- Analysis of working processes and recognition of value-added work
- Kaizen
- Deadlines and results monitoring
- Analysis and organisation of supply
- Polyvalence
- The 7 (8) Wastes of Lean Manufacturing
- Other measures, if required, according to Current State Assessment
What are the benefits of ‘5∆’ method?
- Improvement of productivity and efficiency in production
- Improvement of production quality
- Improvement in logistics efficiency
- Higher level of innovation and establishment of continuous improvement system
- Implementation of performance indicators policies
- Restoring order
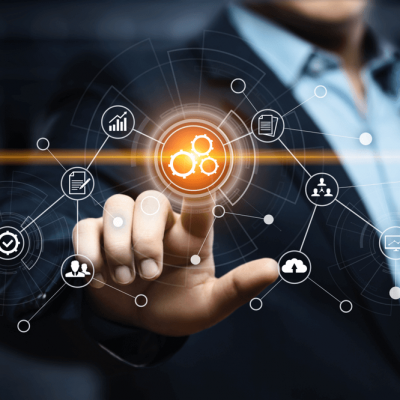